Health & Safety
Our Undisputed Priority.
Safety: Our N°1 Priority
Aperam Takes Pride in its Health and Safety Culture
Simply put, a safety culture is “the way we do things around here.”
We review safety research, learn lessons from incidents in our industry, and consult with our people to develop a framework that defines the critical behaviors that characterize a robust safety culture. This framework helps everyone at Aperam understand the behaviors they should and should not display to play their part in strengthening our safety culture.
Aperam’s corporate health and safety standards help prevent workplace accidents and fatalities. As these standards are only effective when properly implemented, we established our Fatality Prevention Standards (FPS) and Fatality Prevention Audit (FPA) as measures for ensuring compliance.
On top of our continuous monitoring with leading and lagging indicators, our people are actively involved in the design and implementation of our H&S program. We also gather feedback from all employees via our Global Employee Climate Survey.
As a result of these initiatives, all our safety indicators continue to improve. As of 2023, we had a Lost Time Frequency Rate of 2.3, a Total Recordable Incident Rate below 6, and a Severity Rate of 0.14. These good safety results are further boosted by fewer accidents within our new Aperam Recycling perimeter and an increase in potential serious injury situations being reported- to be mitigated- before any inconvenience occurs.
However, we still have a long way to go towards reaching our zero-accident objective. To help, we recently reviewed our Health & Safety organization to strengthen its operational approach, as well as support our sites as closely as possible. The goal is to ensure that Health and Safety is above all a personal value of each employee, whatever the status or function.
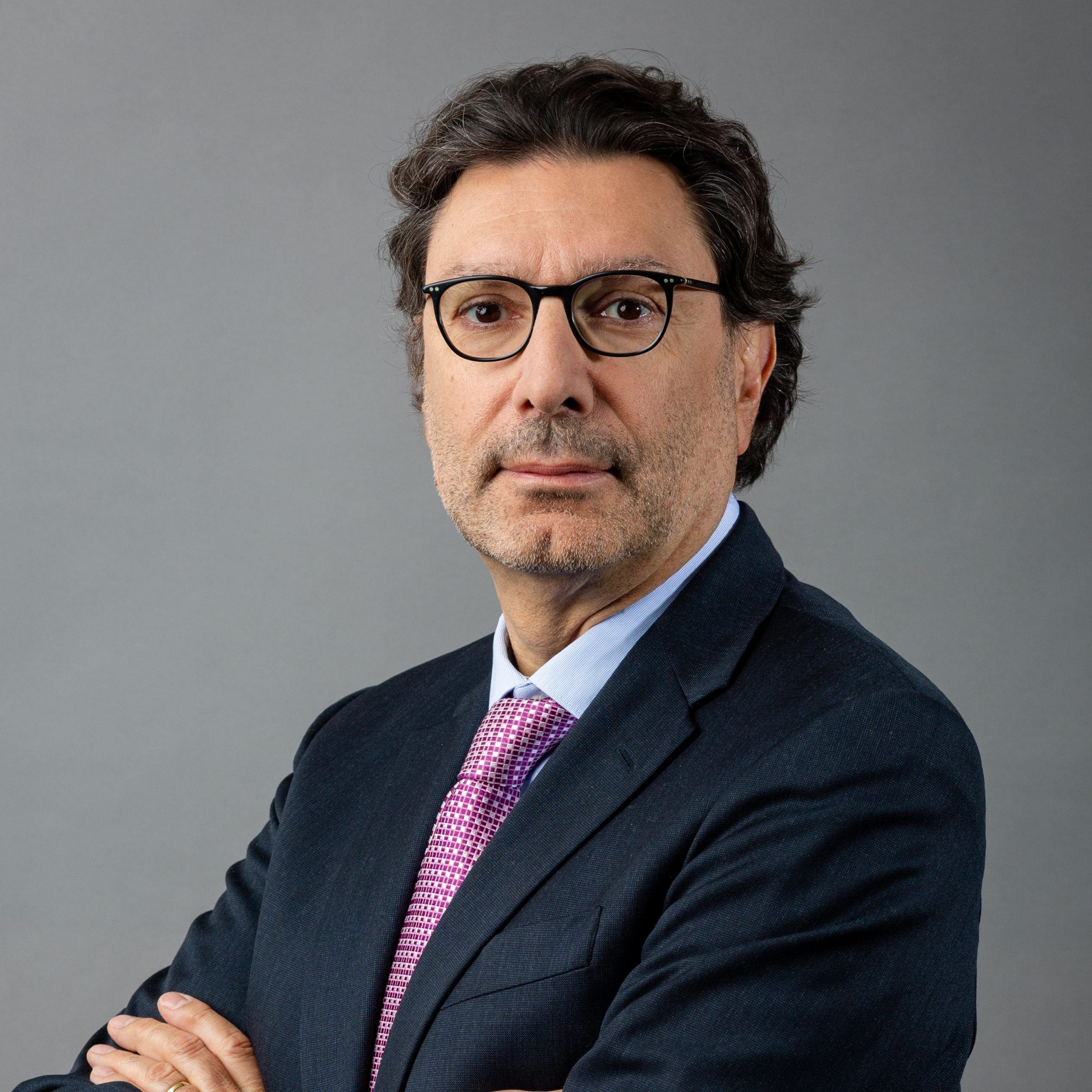
Health & Safety Culture
Building and maintaining a positive health and safety culture helps us and our principal contractors achieve common safety goals.
What is safety culture?
Simply put, a safety culture is “the way we do things around here.” It can also be described as the assumptions, values, attitudes and behaviours related to safety that are shared by a group of people in an organisation. Safety incidents are often associated with failures in safety culture. It is widely accepted that a positive safety culture is vital to achieving excellent safety performance.
What is Aperam doing to improve its safety culture?
We reviewed safety research, lessons from incidents in our industry, and consulted with our people to develop a framework that defines the critical behaviours that characterise a robust safety culture. This framework helps everyone at Aperam understand the behaviours they should and should not display to play their part in strengthening our safety culture.
Why do we focus on behaviours to improve safety culture?
Our efforts to improve safety culture focus on behaviours because we can define, observe and measure them. We also have the right tools and methods to understand behaviour and reinforce the behaviours we know foster a strong safety culture.
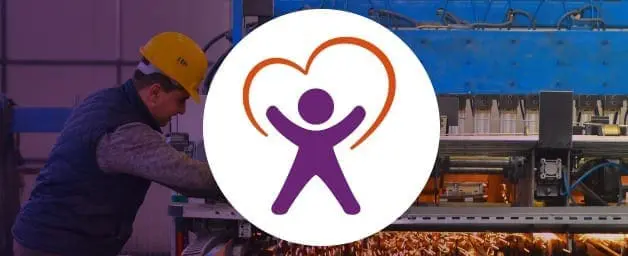
Health & Safety Standards
Together, Aperam’s corporate health and safety standards help prevent workplace accidents and fatalities. As these standards are only effective when properly implemented, we established our Fatality Prevention Standards (FPS) and Fatality Prevention Audit (FPA) as measures for ensuring compliance.
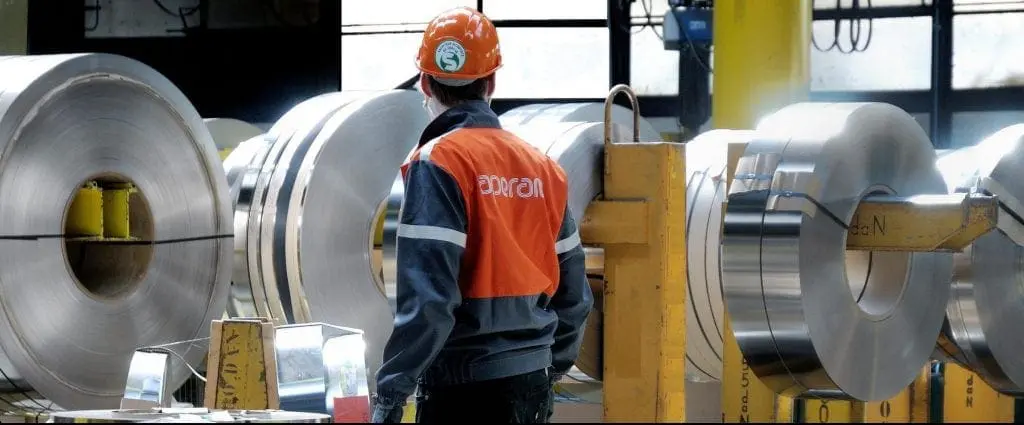
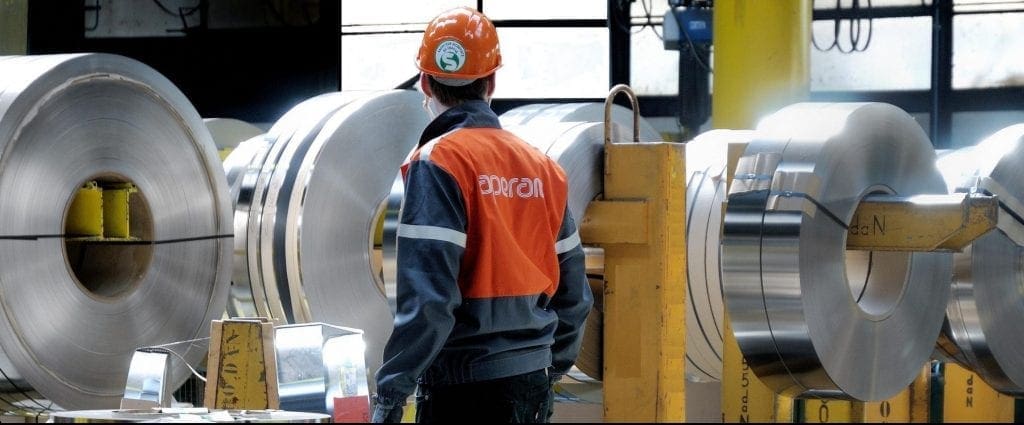
Health: A Local Focus
Due to the diversity of functions, conditions and personnel found across Aperam’s global locations, many of our health initiatives happen at the local level. This strategy ensures that all our standards are tailored to meet the unique health needs of our employees. As a result, every year we see a large variety of local actions happening at each of our units.
Health & Safety Program
Aperam is committed to providing a safe and healthy work environment for all its employees,
contractors and stakeholders and to complying with all existing local laws and regulations.
The key elements of our 2024 Safety Action Plan are:
- Pillar 1- Continue our focus on the sustainable implementation of our ‘Life Saving Standards on
Isolation’, ‘Functional Safety’, ‘Working at Height’ and ‘Contractor Management’ to ensure a fail
safe environment.. - Pillar 2- Full use of our ‘Just Report’ tool for incident reporting, investigation and action tracking
and increase the REX (Return of Experience) diffusion and lessons learned, including a process to
look for transversalities at the site level. - Pillar 3- Strengthening our ‘Safety Culture’ via the deployment of a dedicated training package
developed in-house on Leadership and Coaching Skills (immersion) for all our hierarchical line
functions.
Our 2024 Health Action Plan focuses on the wellbeing of our employees via Pillar 4 of our new paradigm and is a continuation of our Health Roadmap 2022- 2026. It includes a reinforced action plan for 2024 covering:
- Change management, employee assistance program, dedicated training, well-being at work and
resilience. - Define best practices on how to prepare for a return to work after a long absence and on the
promotion of a healthy lifestyle. - Risk prevention (cardiovascular, etc.), dedicated communication plan about mental health
awareness, promoting a stigma-free and supportive work environment. - Physical health and promotion of a healthy lifestyle via standards and awareness campaigns.
We are confident that adhering to this Health and Safety Policy WILL lead us to our goal of becoming a ‘Sustainably Safe Company’.
H&S Awards
To continuously enhance the safety of our sites, Aperam has internal initiatives aimed at promoting successful teams and sharing best practices. In addition to these company initiatives, in recent years many sites also competed in local challenges, including:
- 2023 ISSF Safety Award.
- In Europe, for the sixth year in a row, Aperam was ranked amongst the best employers
(6th place) within Heavy Industry and Materials by French Capital Magazine. - In Brazil, Aperam BioEnergia won the fourth title in the “Incredible Places to Work” 2023
award among Agribusiness companies, and, in the Steel and Mining sector, Aperam
South America came in second place with a consistent result, as in 2022.
- In Europe, for the sixth year in a row, Aperam was ranked amongst the best employers
- 2020 ISSF Safety Award. Our “Think Outside Your Chair!” initiative was noted for its focus on promoting the health and well-being of our employees. The campaign provides employees with quick and easy exercises for preventing injuries, improving posture, increasing flexibility and supplying necessary nutrients to the muscles and brain. Read more
- 2019 ISSF Safety Award. Aperam was recognised with a Safety award at the ISSF Annual Awards ceremony for its “Leave your phone in your locker!” project.
- 2018 ISSF Safety Award. The International Stainless Steel Forum (ISSF) awarded Aperam its Silver Safety Award. The award recognises Aperam’s successful SAFE programme.
- 2017 Health & Safety Awards. In our 2016 Sustainability Report we highlighted the work done by Aperam Genk to reduce accidents and improve controls and safety in transport fleets, with very significant results and some carriers banned. Since then, this programme won the second prize at the annual International Stainless Steel Forum, thanks to its multifaceted approach and engagement with all parties involved. As ISSF commented: “This is a timely reminder that our safety programmes are not confined only to the plants, but extend outwards along the routes taken by our transport.”
- GESiM’s Special Prize, won in 2016 by a 12 member delegation from the Gueugnon rolling mill for their idea for enhancing the process used to change grinding wheels for rectification.
- The Regional and National Competition organised by the Polish Labour Relation Commission recognises the best safety conditions at work. Out of 17 pre-selected finalists, Aperam’s Poland Service Centre took home the prize.
- German BGHW 2016 Prevention Award, given to our German unit for their “Safe working on factory roofs” project. The team was selected from 60 applications.