Waste & Recycling
Home Sustainability Environment Waste & Recycling
Environmental Sustainability
From recovering the metallic content of our melting shop dust to our commitment to becoming a zero-waste company, it’s no stretch to say that Aperam is a recycling champion. We also endlessly promote the use of secondary resources over primary materials and the recycling of all types of waste.
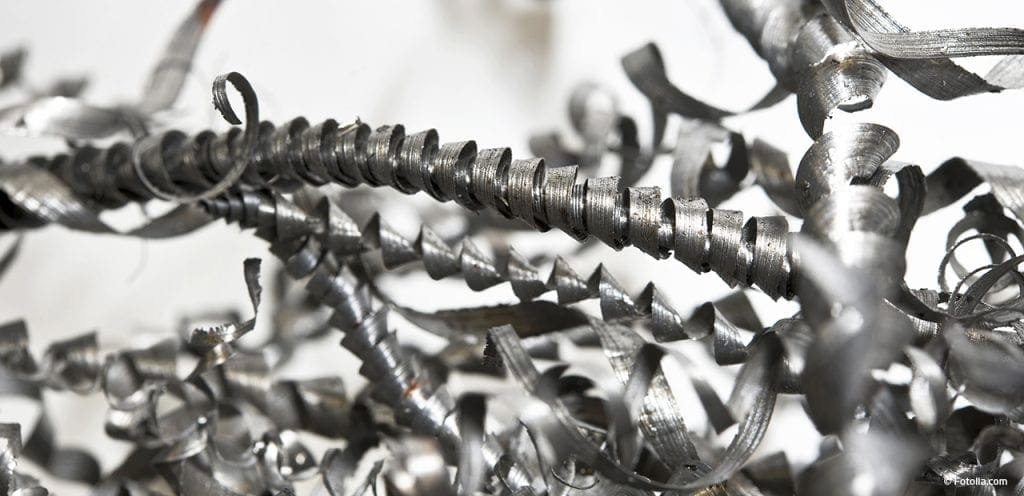
Responsible Manufacturing from Recycled Materials
This is why we use as much scrap as possible when making our products. On average, Aperam’s products, including those made in Brazil (where the scrap market is nearly nonexistent) contain 65% metallic scrap. At our European sites, that figure is 88.5%, with some of our austenitics produced at the Genk facility recording scrap rates of over 95%.
Furthermore, as an active promoter of a circular economy, we not only recycle scrap into our production, but a range of external waste too. As of 2023, 29% of all our material (including nitrogen, fuel, wooden pallets, consumables, etc.) came from recycled sources.
Recycling Our Waste and By-products to become a Zero-Waste Company
One of our responses to this challenge is Recyco, our European recycling unit dedicated to recovering and treating the metallic content from melting shop dust and sludge. Re-using the furnace of a former melt shop, we treat these residues and extract the valuable metallic content to send it back for reuse.
However, some by-products, such as acids and specific treatment mud, still need a viable technical solution. That’s why our engineers and R&D team are working on innovative new solutions to neutralize such hazardous waste. As of 2020, around 6% of our total waste was classified as hazardous.
On our path to becoming a zero-waste (for landfill) company, we report that we currently send just 6.9% of our by-products to the landfill, with the remainder being reused, recycled or stored for future recycling. As a result, our waste recovery ratio now stands at 93.1%.
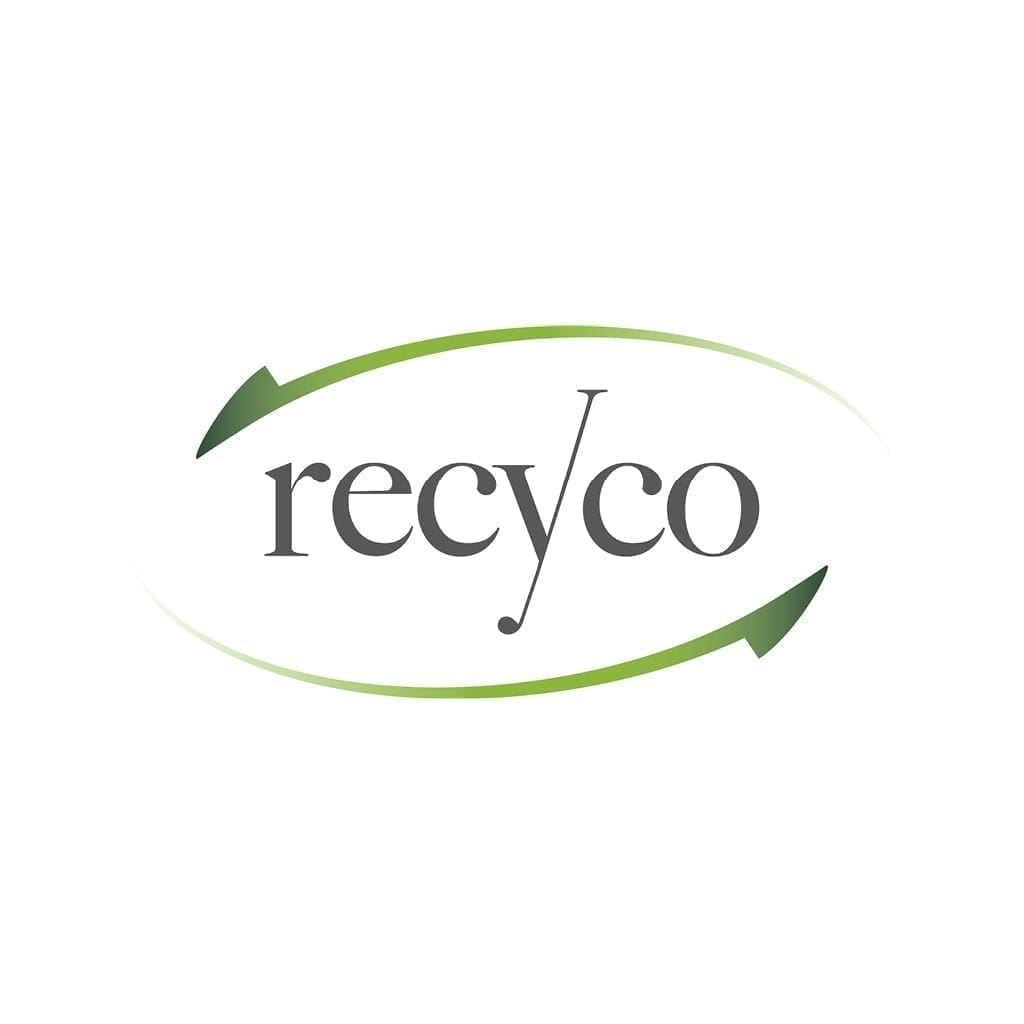